Centrifugal cast ductile iron pipe and fittings
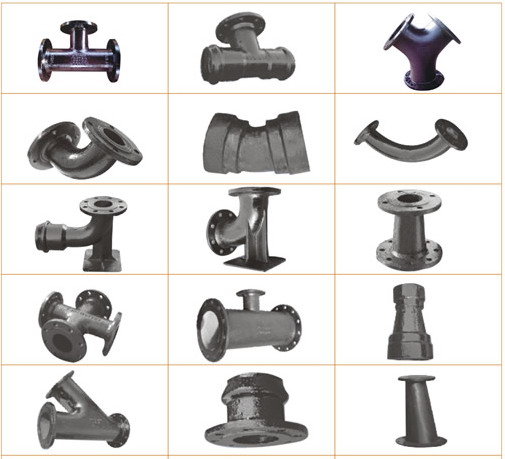
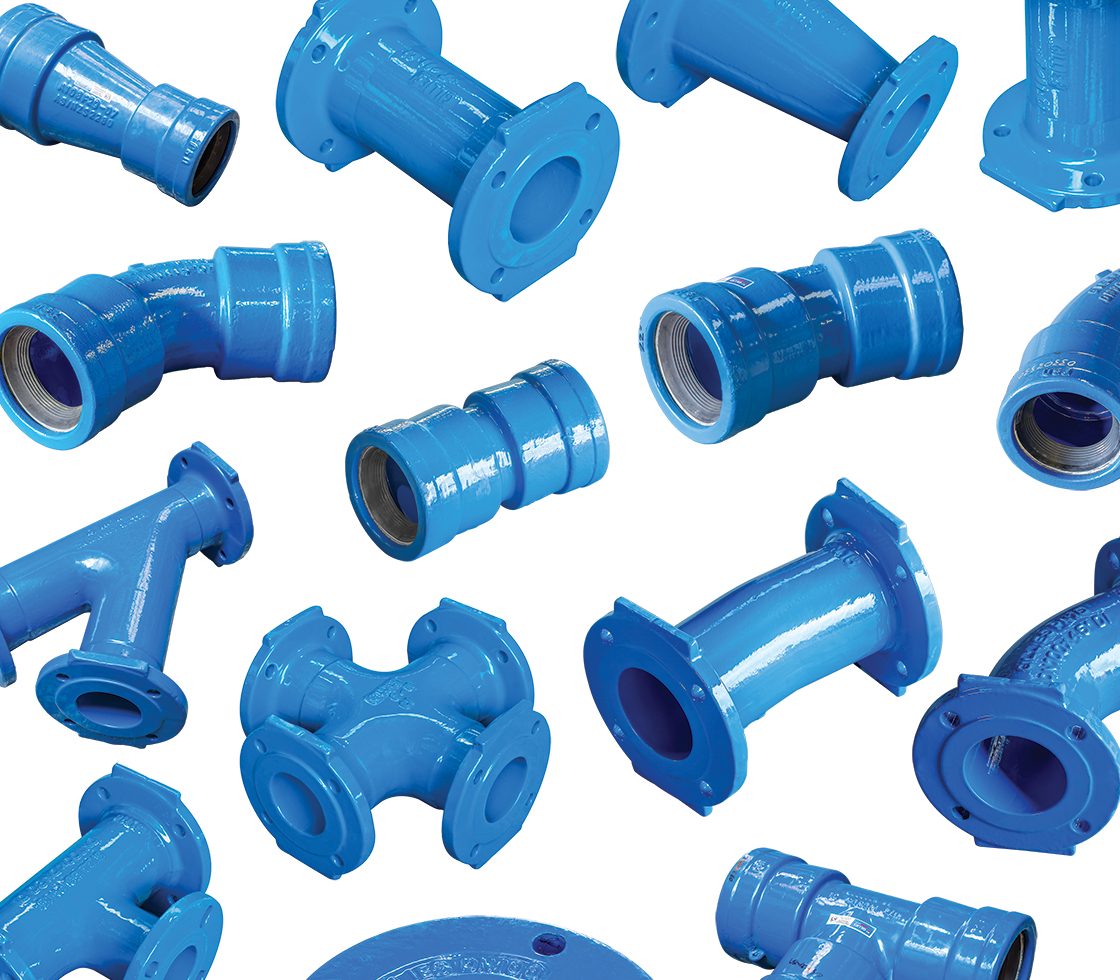
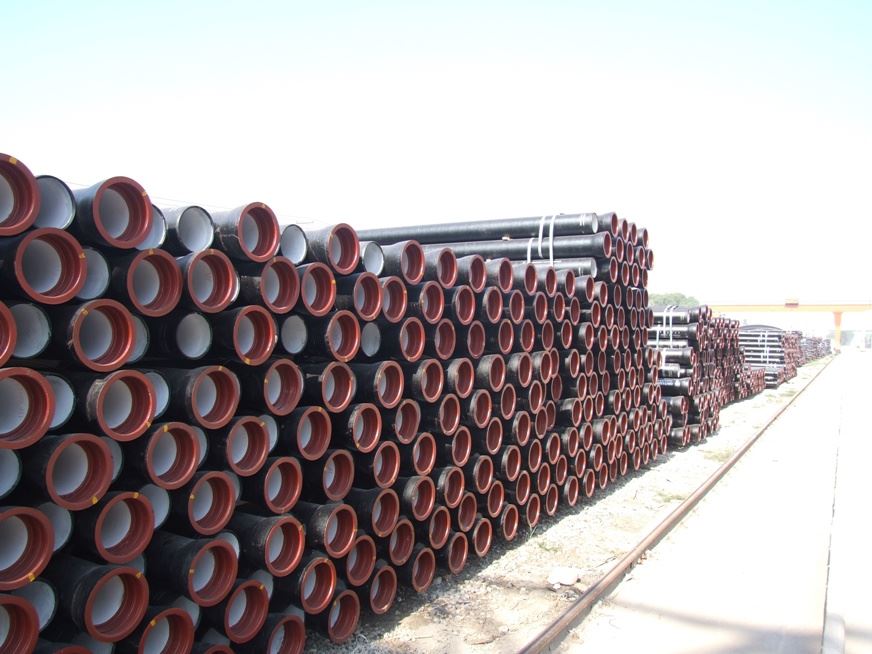
Ductile iron pipe&fittings:
1 | Certificate | ISO9001/WRAS/SGS |
2 | Internal coating | a). Portland cement mortar lining |
b). Sulphate resistant cement mortar lining | ||
c). High-Aluminum cement mortar lining | ||
d). Fusion bonded epoxy coating | ||
e). Liquid epoxy painting | ||
f). Black bitumen painting | ||
4 | External coating | a). Zinc+bitumen(70microns) painting |
b). Fusion bonded epoxy coating | ||
c). Zinc-aluminum alloy+liquid epoxy painting |
Comparison of properties:
Ductile iron pipe class 30 | |||
Item | D. I. pipe | G. I. pipe | Steel pipe |
Tensile strength(N/mm2 ) | ≥ 420 | 150-260 | ≥ 400 |
Bending strength(N/mm2 ) | ≥ 590 | 200-360 | ≥ 400 |
Elongation(%) | ≥ 10(DN40-1000) | 0 | ≥ 18 |
Elasticity coefficient(N/mm2) | Approx.16× 104 | Approx.11× 104 | Approx.16× 104 |
Hardness(HB) | ≤ 230 | ≤ 230 | Approx.140 |
Corrosion resistance after 90 days(g/cm2 ) | 0.0090 | 0.0103 | 0.0273-0.0396 |
Centrifugally cast ductile iron pipe are made from spherical graphite cast iron by centrifugal spinning process.The pipes, which can convey many fluid media such as water,oil and gas,are widely used in various pipeline projects for metallurgy,mine,water conservancy,petroleum and urban public service utility.
1.Possessing high strength, good toughness as steel and better corrosion resistance than steel,that can help them withstand shock encountered during transportation, installation, handling and use.
2.The ductile iron pipe is the ideal substitute for gray cast iron pipe and common steel pipe.
3.The DI pipes are produced with good straightness, even wall thickness, high dimension accuracy, smooth surface finishing and remarkable mechanical properties, plus with firmly sticking internal & external coating layer.
4.Flexible Push-in joint and rubber gasket are used resulting in convenient installation of pipelines.
5.They are a more sustainable choice, as they’re usually made from recycled materials, which is a feature highlight from an environmental perspective
6.Inside diameters are larger than most, increasing flow, which reduces energy consumption and pumping costs over time
7.They have a high bursting strength, which is suitable for high pressure applications.